Design for 3D printing,
simplified.
Our software makes it simple for businesses to unlock this potential.
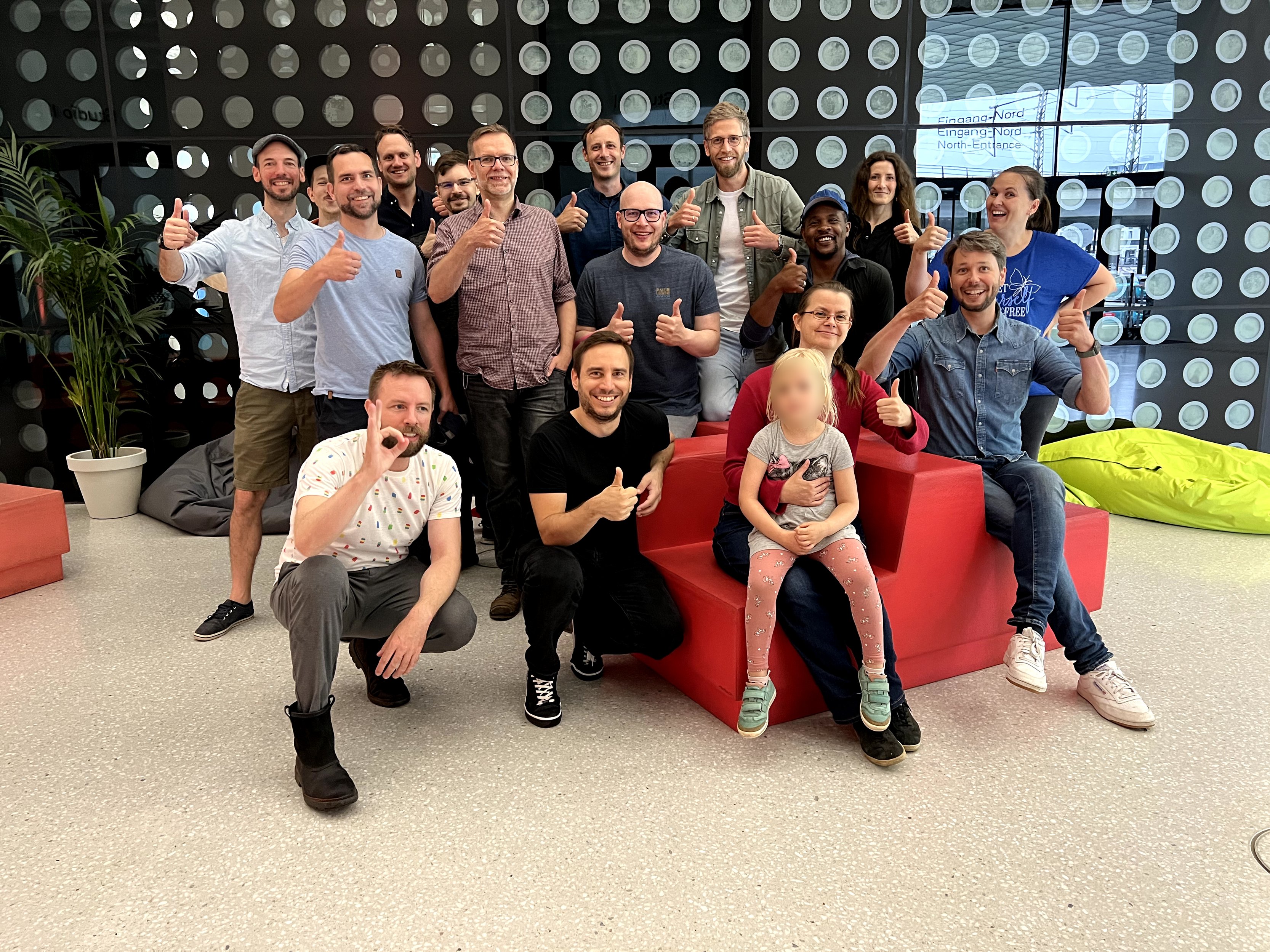
About trinckle
Located in Berlin, trinckle is at the forefront of developing software solutions for additive manufacturing (or 3D printing, as it's commonly known).
Our flagship offering, paramate, revolutionizes design workflows and introduces an intuitive platform for smart product configuration.
paramate
paramate makes it easy to personalize products, whether it's a special fit for medical devices, improved tools for factories, or unique items for everyday life.
Through powerful algorithms, paramate simplifies and streamlines the design process, so you don't need to be an expert to create or modify designs.
Founding team
"Customization is the killer application of 3D printing."
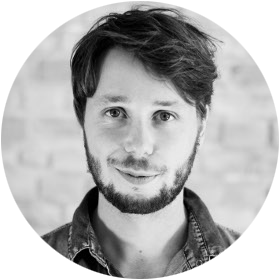
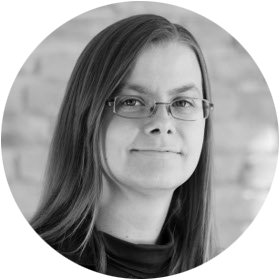
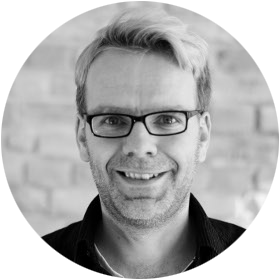
Company culture
Curiosity fuels creativity
We motivate our team to remain open to new and unexpected possibilities. This helps us to develop standout products that offer exceptional value to our clients.
Innovation meets perfection
We believe in agile development, challenging the status quo, and always pushing our limits. This drive ensures we offer our clients the best solutions.
Custom user experiences
We specialize in customization.
By collaborating closely with our clients, we understand their objectives, ensuring both they and their customers get the perfect solution.
Open communication
Whether within our team or when working with clients, our partnerships are built on trust and openness. We pride ourselves on being a reliable, trust-worthy partner.
Many hands make light work
Teamwork is so important to us.
We combine the extensive and diverse skill sets of our team to guarantee the best results for our clients.
Pushing the boundaries: trinckle research
With paramate, we create new products and ways of doing business for our customers.
To make sure we're offering the best and latest products, we're continuously pushing boundaries by contributing to selected research projects.
ProAStra Dental
is a project of trinckle together with the TU Berlin (IWF) and the Charité (IZMK) in the period from 01.01.2023 to 31.12.2025.
The goal is an automated process chain for the production of novel dental implants. Exemplary key innovations are the digital workflow for implant adaptation, the additive-subtractive manufacturing process, the implant fixation in the bone and the surgical process.
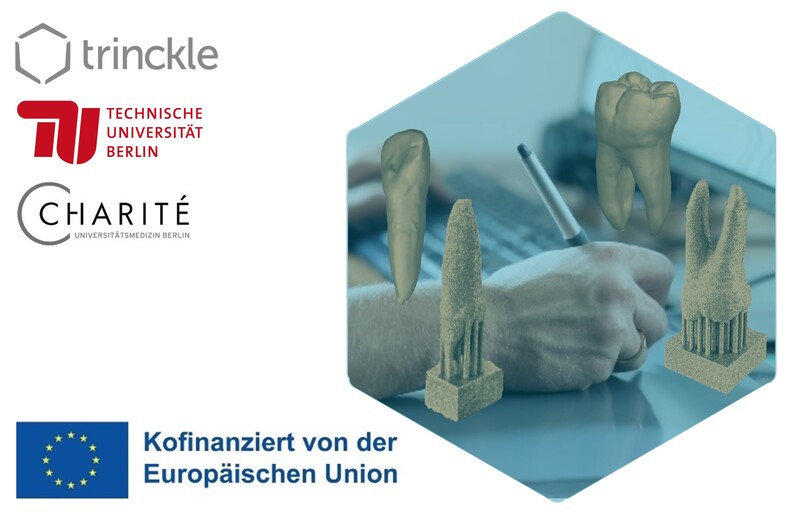